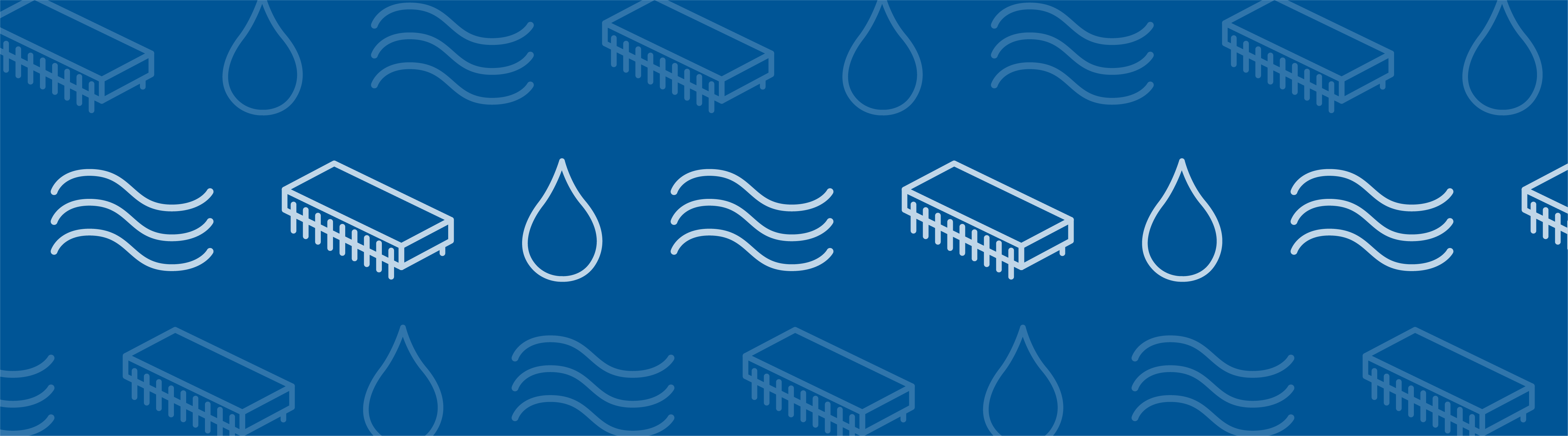
Microfluidic devices are so small that the micropumps and micromixers that control and mix the fluid inside the device cannot involve any moving components. Instead, they must take advantage of electroosmotic flow. Here, I will describe the concept of electroosmosis and the electrical double layer (EDL), and how to model these in COMSOL, walking you through two example models.
Microfluidic Devices Require Pumps and Mixers without Moving Parts
Microfluidic lab-on-a-chip systems have played a major role in recent years in shrinking the size of conventional lab-scale chemical and biological analyses to a chip-format that is millimeters to a few centimeters in size. These devices are often referred to as micro-total-analysis-systems (μTAS) and have profound applications in medical diagnostics, drug testing and delivery, forensic analysis, DNA analysis, and even immunoassays and toxicity monitoring. These devices offer many advantages such as point-of-care testing (POCT) and diagnostics due to their extremely small device size. The fact that they require a smaller volume of fluids is suitable for situations where samples are not available in large volumes or when reagents are expensive. These devices can also process multiple samples at once (referred to as parallel processing) and have low power requirement.
On-board mixing and control of fluid is important in a typical lab-on-a-chip system and often these systems require micropumps to control the fluid flow inside the channels and micromixers to accelerate the mixing process. The size of the fluid channels in these microchips typically varies between 1 µm and 500 µm. At these length scales, it is not practical to use any moving parts to build the pumps and mixers. Devices without moving parts are also more reliable. So how do you activate the flow without any moving parts? The answer is: Electroosmosis.
What “Electroosmosis” Means
In the field of microfluidics, the flow is often driven by an electric field. By definition, electroosmosis refers to the motion of a liquid induced by an applied potential across a microchannel. Driving the flow with an electric field allows for the fabrication of pumps and mixers without moving parts.
What drives the electroosmotic flow?
To get a better understanding of how the flow is driven by an electric field, we first have to understand what happens very close to the walls inside the microchannels, at the fluid-solid interface. The majority of lab-on-a-chip devices are made out of silicon glass. When in contact with the fluid (it can be water or any buffered solution), the glass surface participates in acid-base reactions and ion exchange — we will refer to this complex process as surface chemistry. Because of surface chemistry, the glass surface acquires a negative density charge. The concept of electrical double layer (EDL) has been introduced as a continuum description of this surface chemistry at the walls. It reflects an unequal distribution of charges (ions) at the fluid-solid interface and consists of two layers surrounding the object:
- The first layer, known as the surface charge layer, is made of ions absorbed in the surface due to chemical reactions (negative charges in this case).
- The second layer, known as the diffusive layer, is made of free ions attracted to the surface due to the influence of electric attraction and thermal motion. This second layer screens the surface charge and its net charge is equal to the surface charge, but has the opposite polarity.
Electrical double layer (EDL).
The EDL structure is summarized in the figure above, showing the distribution of ions as a function of the distance to the glass wall, as well as the potential (blue line on top) in the EDL versus a point in the electroneutral bulk. If we take a closer look at the diffusive layer, we notice that it can be further split into two parts that are separated by a slipping plane. This plane separates the immobile fluid on the left (attached to the surface), from the fluid that is free to move under the influence of tangential stress. An electric field can then be used to induce the motion of the net charge in the EDL due to the Coulomb force. Further away from the wall is the third layer, the electroneutral bulk.
Since it’s difficult to make any kind of measurement in microfluidic channels without disrupting the flow, these chips are often analyzed from a computational point of view. How can we model this using simulation software?
Modeling of the Electrical Double Layer (EDL)
Three physics are involved in this problem:
- The electrostatics physics contains the equations, boundary conditions, and space charges for solving for the electric potential. The electric field is recovered from the gradients of the potential field (E=-\nabla V). The space charge is obtained by summing up the contribution of the anions and the cations. The concentration of these ions is computed by the Transport of Diluted Species interface.
- The Transport of Diluted Species interface solves for the mass transport of diluted species in mixtures, solving for the species concentrations. It simulates chemical species transport through diffusion (Fick’s law), migration (when coupled to an electric field. In this case, the electrical field is computed by the Electrostatics interface), and convection (when coupled to fluid flow. Here, the fluid flow is computed by the Laminar flow interface.)
- The Laminar flow interface has the equations, boundary conditions, and volume forces for modeling freely moving fluids using the Navier-Stokes equations, solving for the velocity field and the pressure. The volume force, \rho_{e} E, where \rho_{e} is the electric charge density, is computed by the Electrostatics interface.
The thickness of the EDL is generally around a few nanometers and the concentration of the ions varies exponentially close to the wall. Since the thickness of the EDL is so small, it can be advantageous to use an approximation in this region. COMSOL includes an electroosmotic velocity boundary condition that ignores the flow field between the wall and the slipping plane, and analytically computes the velocity at the wall based on the zeta potential using the Helmholtz-Smoluchowski relation:
The resulting models will have significantly lower computational requirements. This is a very useful approach for many practical engineering applications.
Therefore, we recommend that you first calculate the Debye length, i.e. the length of the EDL, before you set up the model using COMSOL Multiphysics. If this length is much smaller than your geometrical length scale, use the electroosmotic velocity boundary condition. If not, use the traditional no-slip velocity wall boundary condition and resolve the flow in the EDL. Remember that concentration varies exponentially with potential in the double layers; a fine boundary layer mesh is necessary to resolve the abrupt change in the double layers if the electroosmotic velocity boundary condition is not used.
In the next section I will show you two examples where this applies. The first example is of a micropump that is resolved in the whole geometry, including the EDL. The second example, a micromixer, uses the electroosmotic velocity boundary condition.
Applications
Example 1: Micropumps
In this example, the top and bottom walls of the microchannel (length 60 nm, height 10 nm) are negatively charged (-0.02 C/m^{2}) and electrodes are used at the inlet (left boundary, 6 mV) and outlet (right boundary, 0 V) to drive the flow. The resulting electric potential, space charge distribution, and velocity field are shown below:
Plot visualizing the electric potential computed by the electrostatics physics.
Plot depicting the net space charge, i.e. the contribution of the anions and the cations. The positive net charge screens the negatively charged wall.
Velocity plot showing the motion of the net charge in the EDL due to the Coulomb force.
In order to introduce the next example, the micromixer, let’s first see what happens when sections of the top and bottom glass walls (shown in blue in the next plot) are positively charged (0.06 C/m^{2}) instead of negatively charged:
The results for the electric potential, space charge, and velocity field follow:
![]() |
![]() |
![]() |
While the space charge is positive around negatively charged walls, it is negative around the positively charged portions. The inversion of the space charge leads to an opposite electroosmotic velocity close to the wall. This opposite near-wall velocity leads to the introduction of a swirl in the channel (as seen in the streamline patterns), which could be used to mix different chemical species.
Example 2: Micromixers
At the microscale, flow is usually a highly ordered laminar flow, and the lack of turbulence makes diffusion the primary mechanism for mixing. While diffusional mixing of small molecules (and therefore of rapidly diffusing species) can occur in a matter of seconds over distances of tens of micrometers, mixing of larger molecules such as peptides, proteins, and high molecular-weight nucleic acids can require equilibration times from minutes to hours over comparable distances. Such delays are impractically long for many chemical analyses. These problems have led to an intense search for more efficient mixers for microfluidic systems. In the following example, the walls are negatively charged, as in the micropump example we just went over, and electrodes are used at the inlet (left boundary) and outlet (right boundary) to drive the flow. To introduce some mixing, four additional electrodes are placed on the walls of the mixing chamber. These four electrodes induce a fluctuating electroosmotic velocity at the wall:
Plot exemplifying how the mixer operates. Two fluids with different concentrations are
used at the inlet to study the mixing process.
When the electric field is not applied, the flow is laminar and the diffusion coefficient is very small, so the two fluids are well separated at the outlet.
When the alternating electric field is applied, the mixing increases considerably, owing to the alternating swirls in the flow.
Concluding Thoughts and Next Steps
This blog post briefly described electroosmotic flow and the concept of the electrical double layer. You also learned how to model this type of problem within the COMSOL environment. If you want even more information about the Electroosmotic Micromixer model, you can download the model and model documentation from our Model Gallery. You can get a general overview of COMSOL’s microfluidics modeling capabilities here, or contact us for more in-depth information on how you can use COMSOL Multiphysics to model a variety of applications.
Finally, don’t forget that COMSOL is a multiphysics software, allowing you to couple the physics seen in this model to other physics. Adding the particle tracing physics, for instance, would allow you to model electrokinetic phenomena such as electrophoresis and dielectrophoresis.
Comments (17)
Bao Ho Dang
February 1, 2016Thank you for the nice post. I have a question: Where in the model can I see the coupled volume force (rho_e*E)?
Jose Mena
September 14, 2016you can send me the model the example 1 (micropumps) of Modeling Electroosmotic Flow and the Electrical Double Layer, Fabrice Schlegel. Thank you!
My E-Mail: jflores@ece.buap.mx
Caty Fairclough
September 14, 2016Hi Bao and Jose,
Thank you for your comments and for your interest in this blog post. For both of your requests, I’d suggest reaching out to our support team.
Online support center: https://www.comsol.com/support
Email: support@comsol.com
Best,
Caty
Gábor Járvás
January 5, 2017Hi Caty,
thanks for this useful example! I got the model from the Support and tried to modified it with adding additional force convection i.e. define few pascal pressure at inlet boundary condition of laminar flow model. However, after this modification it can not be solved. Is there any trick how to do this?
Thanks,
Gabor
Caty Fairclough
January 5, 2017Hi Gabor,
Thank you for your question! Laminar flow, electrostatics, and charge transport form a highly nonlinear system, so small changes to the input parameters can drastically affect the nonlinearity of the equations. This means that convergence is more difficult to obtain.
One thing you can try is to ramp up the inlet pressure using an “Auxiliary sweep” in the study settings. If you still have trouble obtaining convergence, I would recommend sending the model to support@comsol.com.
Thanks,
Caty
KIRAN P B
January 20, 2017hi
KIRAN P B
January 20, 2017can some one post the Analysis of Electroosmotic Flow of Power-law Fluids in a Microchannel(1D)
KIRAN P B
January 20, 2017https://www.comsol.co.in/paper/download/152697/srinithin_poster.pdf
this is my model
Caty Fairclough
January 20, 2017Hi Kiran,
Thanks for your comments. For answers to your modeling questions, I suggest reaching out to COMSOL Support.
Online support center: https://www.comsol.com/support
Email: support@comsol.com
Thank you!
Best,
Caty
Arputha Paul
June 2, 2017Hi,
I need the model for Example 1, the micro pump. I contacted the support team, but unfortunately they could not provide me with the model. Does anyone have it here?
Many Thanks and Regards,
Arputha
Caty Fairclough
June 12, 2017Hi Arputha,
Thanks for your comment.
While that specific model file is not available, we do encourage you to browse other microfluidics examples in our Application Gallery: https://www.comsol.com/models/microfluidics-module.
Paresa Modarres
June 28, 2017Hi,
In example 2, when we are defining wall1 properties, we choose electroosmotic slip for all faces of the wall. Why is that? Shouldn’t the electroosmotic slip be only on top of the electrodes and not anywhere else?
Bridget Cunningham
July 19, 2017 COMSOL EmployeeHi Paresa,
Thank you for your comment.
In the electroosmotic mixer model, the tangential electric field, which is responsible for the fluid slip, is present on all boundaries, not just the electrodes. In fact, since the electric potential does not vary spatially on the electrodes themselves, the slip velocity will be zero. The boundaries between the electrodes will have the maximum slip velocity.
Anindita Bhattacharya
September 18, 2017Hi,
I have been facing issues trying to model streaming potential instead of electrosmotic flow. How can I get votage as the output? Do I have to describe electric currents module in addition to what is described here?
Best Regards
Anindita
Bishwajit Nandi
August 18, 2022you can send me the model the example 1 (micropumps) of Modeling Electroosmotic Flow and the Electrical Double Layer, Fabrice Schlegel. Thank you!
My email id : bishwajitdgp@gmail.com
ABHIJIT LINCON
January 27, 2025you can send me the model the example 1 (micropumps) of Modeling Electroosmotic Flow and the Electrical Double Layer, Fabrice Schlegel. Thank you!
My mail id: ablincoln44@gmail.com
Yihang Chen
June 7, 2025Can you send me the model the example 1 (micropumps) of Modeling Electroosmotic Flow and the Electrical Double Layer, Fabrice Schlegel. Thank you!
My email id : yihangch@kth.se